Your Industrial Epoxy Flooring Is Slowing You Down
In industrial facilities across Greenville, epoxy flooring is a common sight. It’s durable, easy to clean, and affordable—at least at first. But over time, many businesses are discovering the hidden costs of outdated or poorly installed epoxy floors. From peeling surfaces to costly shutdowns, the wrong flooring system can slow down productivity and increase maintenance expenses.
If your operations rely on efficiency, safety, and minimal downtime, your epoxy flooring might be holding you back more than helping. In this guide, we’ll uncover why standard epoxy systems fail in high-demand environments, what smarter alternatives exist, and how
Zachary Daniel Concrete helps industrial clients in Greenville upgrade without disrupting operations.
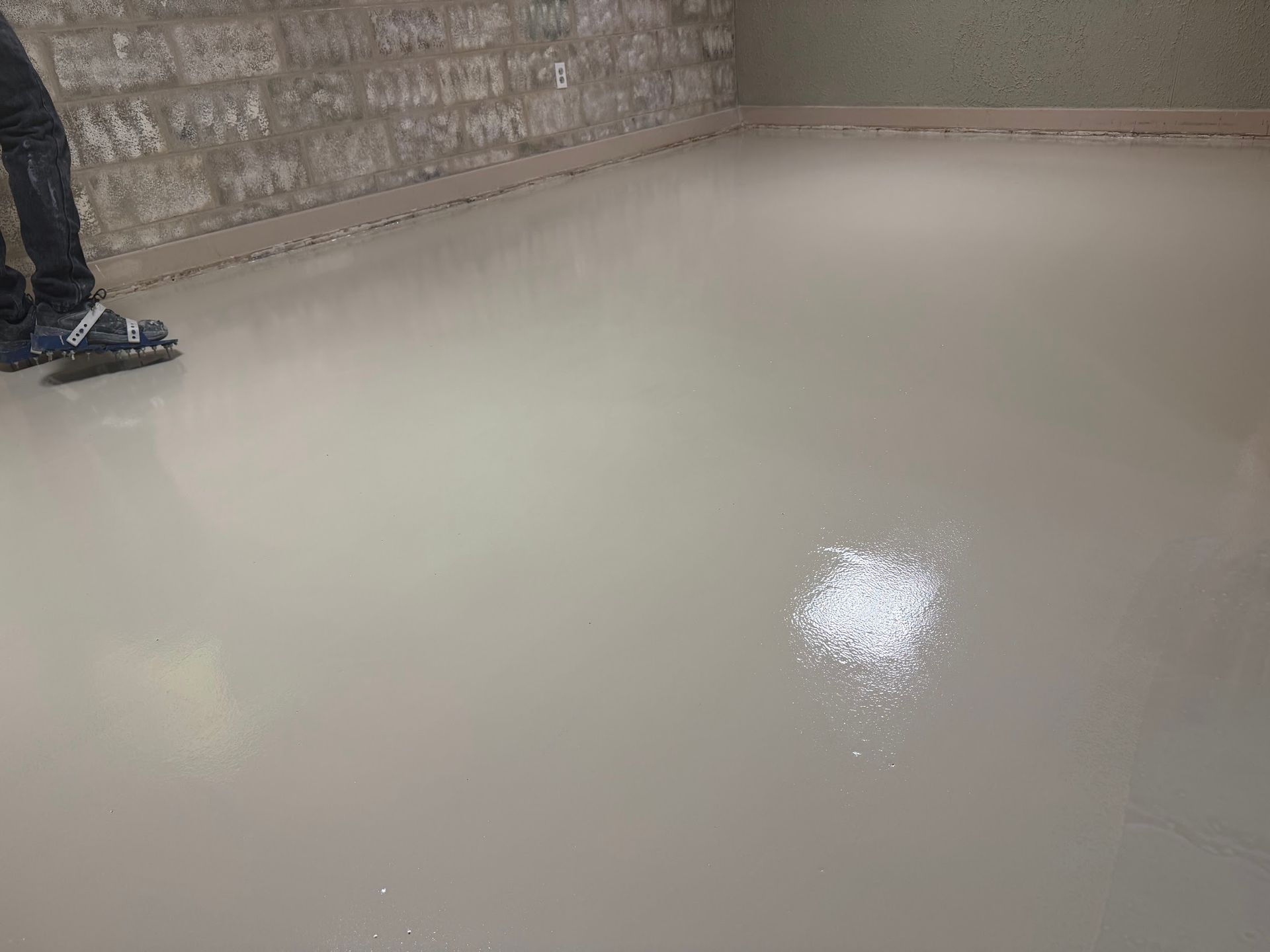
Why Epoxy Floors Fail in Industrial Environments
Epoxy has been the go-to for industrial flooring for decades. But many facilities in Greenville are now dealing with the consequences of choosing systems that weren’t designed for long-term, high-stress use.
1. Moisture Problems
Concrete slabs can hold moisture, and if the epoxy wasn’t installed with proper vapor barriers, the result is bubbling, peeling, and delamination. This often leads to expensive repairs—or worse, complete replacement.
2. Chemical Exposure
Factories, warehouses, and processing plants use harsh chemicals daily. Many basic epoxy coatings are not designed to withstand repeated exposure, leading to discoloration, softening, and floor degradation.
3. Thermal Shock and Heavy Loads
Epoxy systems break down under extreme temperature changes or impact from heavy equipment. Forklift traffic, dropped tools, or even cleaning with hot water can cause cracking and chipping.
4. Downtime for Repairs
Every hour your floor is down costs money. Basic epoxy floors often need reapplication or patching that requires shutting down operations for 24–72 hours—an unnecessary burden in fast-paced environments.
The Hidden Costs of “Affordable” Epoxy
On paper, epoxy coatings look like a budget-friendly solution. But the long-term costs quickly add up:
- Frequent repairs
- Lost revenue from shutdowns
- Safety risks from slick or damaged surfaces
- Damage to equipment due to uneven flooring
- Negative impressions during audits or client walkthroughs
What seemed like a cost-saving move becomes a recurring liability.
What to Use Instead: Smarter Industrial Flooring Options
Businesses in Greenville are now looking beyond basic epoxy for stronger, faster-curing, and longer-lasting alternatives. At Zachary Daniel Concrete, we recommend industrial-grade systems that are customized for your operations—not just coated on top.
Polyaspartic Coatings
Polyaspartic systems cure quickly (often in under 24 hours) and resist UV, chemicals, and abrasions better than epoxy. They’re ideal for fast turnarounds with heavy foot or vehicle traffic.
Urethane Cement Systems
These systems handle thermal shock, chemicals, and impact without breaking down. They’re a great choice for food and beverage processing plants, breweries, and pharmaceutical facilities.
Concrete Overlays with Sealers
If your slab is structurally sound but worn, resurfacing with a high-performance overlay and sealer may provide a better finish and more slip resistance than reapplying epoxy.
Moisture Mitigation Systems
For facilities dealing with moisture vapor, we install a mitigation layer before applying any coating to ensure long-term adhesion and durability.
Why Greenville Industrial Businesses Choose Zachary Daniel Concrete
Not all concrete contractors understand the demands of industrial flooring. Here’s why professionals across Greenville trust us:
Tailored Solutions
We never offer one-size-fits-all systems. Every floor we install is based on your environment, traffic, and operational needs.
Downtime-Sensitive Scheduling
We work nights, weekends, or in phases—whatever it takes to minimize disruptions.
Advanced Materials
We only use premium-grade coatings tested for industrial use. Our systems resist heat, moisture, chemicals, and impact.
Safety First
We build flooring with OSHA standards and audit-readiness in mind—from slip resistance to line striping.
Is It Time to Replace Your Epoxy Floor?
If you’re seeing these signs, it’s time for an upgrade:
- Peeling or bubbling areas
- Visible cracks or chips
- Slippery surfaces when wet
- Discoloration or chemical stains
- Recurrent shutdowns for patching
Upgrading your floor can prevent safety incidents, boost productivity, and improve your bottom line.
Conclusion
Old epoxy flooring systems may have worked in the past, but today’s industrial demands require stronger, smarter solutions. At Zachary Daniel Concrete, we help businesses in Greenville eliminate floor-related slowdowns with custom industrial flooring that performs under pressure.
📞
Schedule a free assessment today and get expert advice on the best system for your facility. Don’t let your floors drag your business down—upgrade to flooring that works as hard as you do.
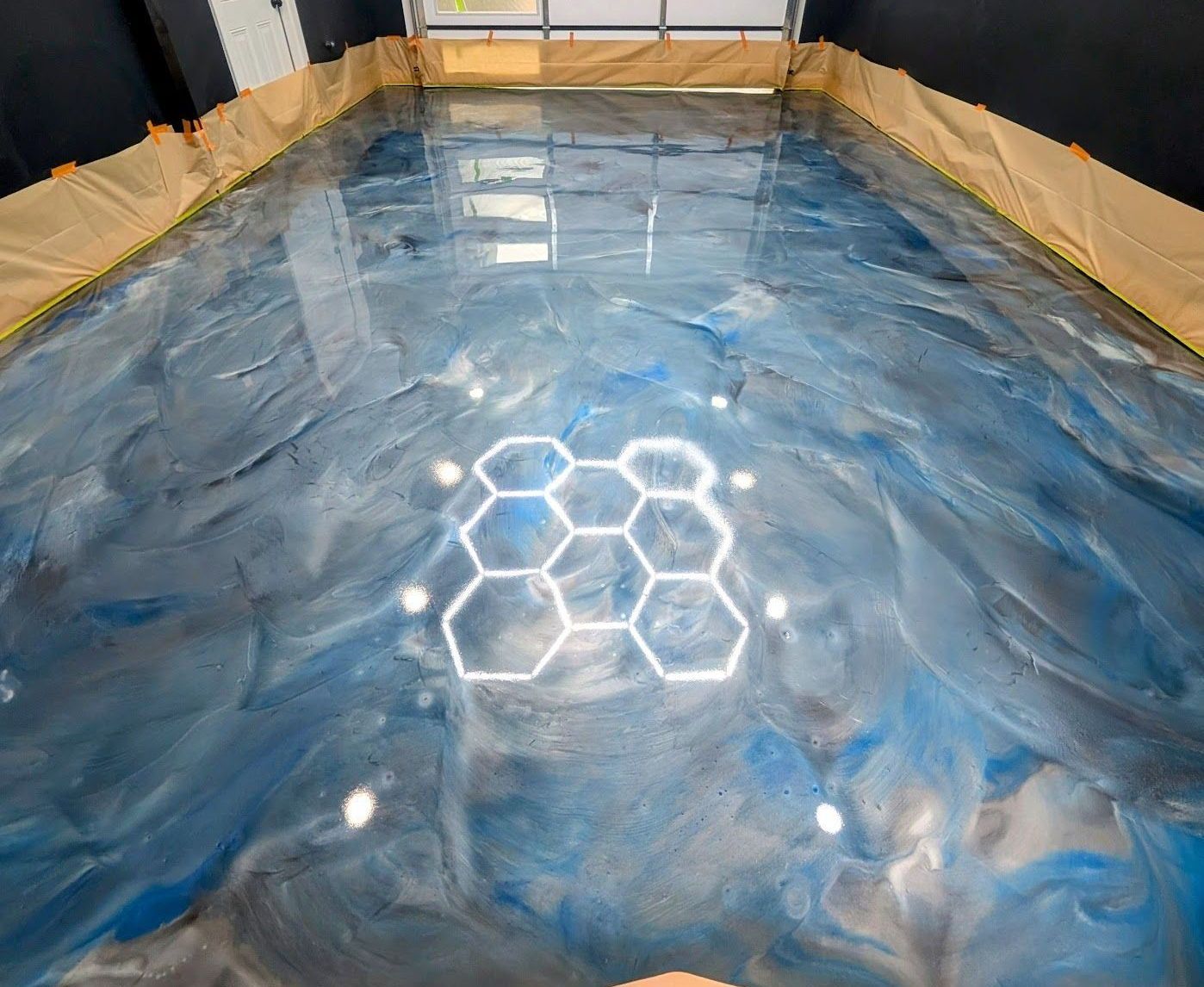